Требования к разработке и изготовлению печатных плат
Рабочая инструкция
1. ЦЕЛЬ
Цель настоящей инструкции – определить требования к печатным платам, связанные с особенностями, которые присущи технологическому процессу сборки изделий на печатных платах и должны быть учтены при разработке и изготовлении печатных плат.
2. ТЕРМИНЫ, ОПРЕДЕЛЕНИЯ И СОКРАЩЕНИЯ
Сокращения, использованные в настоящей инструкции, приведены в Руководстве по качеству.
3. ОТВЕТСТВЕННОСТЬ
За выполнение всех требований настоящей инструкции до передачи КД на единичные печатные платы для технологической подготовки производства отвечает подразделение, разрабатывающее плату.
За контроль выполнения требований к разработке единичных печатных плат и выполнение всех требований настоящей инструкции к групповым заготовкам печатных плат отвечает ОГТ.
За трансляцию требованийнастоящей инструкции поставщикам (производителям) печатных плат и соблюдение имиэтих требований отвечает дирекция по закупкам.
4. ОБЩИЕ ПОЛОЖЕНИЯ
4.1. При топологическом проектировании печатных плат необходимо руководствоваться требованиями и рекомендациями следующих государственных и международных стандартов:
- IPC-2221,
- IPC-2222,
- IPC-2224,
- IPC-SM-782A,
- ГОСТ Р 53429-2009.
4.2. Специальные требования к образам SMD-компонентов в программах разводки топологии печатных плат:
4.2.1. Все образы SMD-компонентов должны иметь точку привязки для автоматического монтажа (Pick and Place). Данная точка вводится по центру тяжести элемента в редакторе корпусов компонентов (P-CAD Pattern Editor) по команде Place – Pick Point. При этом точка привязки для автоматического монтажа (Pick Point) может не совпадать с точкой привязки компонента (Ref Point).
4.2.2. Образы SMD-компонентов должны иметь соответствующие действительности значения атрибутов Type и Value.
4.3. Ширина платы (групповой заготовки печатных плат) от 80 до 250мм.
4.4. Толщина платы от 1 до 3мм.
4.5. Длина платы (групповой заготовки) от 150 до 350 мм.
4.6. Минимальный зазор между проводниками – 0,3 мм.
4.7. Минимальная ширина проводника – 0,3 мм.
4.8. Оптимальные величины зазоров между проводниками печатной платы (равно как и минимальные размеры самих проводников) в каждом случае должны выбираться исходя из требований к изделию.
4.9. При объективной невозможности обеспечить требуемый по предыдущему пункту запас надежности, размеры отдельных зазоров (а также размеры отдельных проводников) должны указываться на чертежах печатных плат в качестве ключевых параметров.
4.10. На платах следует заранее предусматривать специальные площадки для работы контрольного оборудования (внутрисхемное и функциональное тестирование).
4.11. Не допускается располагать сквозные отверстия диаметром более 10 мм и/или металлизированные отверстия диаметром более 1,5 мм в точке с координатами (х=17 мм; у=73 мм), так как точка с этими координатами используется для позиционирования групповой заготовки в технологическом оборудовании (отсчет координат вести от нулевой точки платы в левую сторону).
4.12. На плате (групповой заготовке) проектируется не менее 3 реперных знаков ∅ 2,0 мм. Вокруг реперного знака должна быть обеспечена зона, свободная от защитного фоторезистивного слоя, ∅ 4 мм. Минимальное расстояние от центра реперного знака до края платы – 6 мм.
4.13. Расположение (несимметричное!) реперных знаков на печатной плате (групповой заготовке) должно обеспечивать возможность автоматического обнаружения поворота платы на 180°.
4.14. Расположение реперных знаков на разных сторонах печатной платы (групповой заготовки) с двусторонним расположением SMD-компонентов должно обеспечивать возможность автоматического обнаружения переворота платы.
4.15. Расположение реперных знаков должно обеспечивать возможность автоматического обнаружения печатных плат разной топологии при одинаковых габаритных размерах (достигается дополнительным смещением одного из знаков на 10 мм для каждого из вариантов топологий плат).
4.16. При мультиплицировании плат, необходимо предусматривать линии скрайбирования модулей.
4.17. Остаточная толщина платы в месте скрайбирования (web) должна быть максимально близкой к 1/3 толщины самой платы.
4.18. Линии скрайбирования должны быть прямыми и проходить от одного края панели к другому через всю панель. Допуск на обработку контура при скрайбировании +/- 0,1 мм.
4.19. Расхождение между линиями скрайбирования с разных сторон платы – не более 0,1 мм.
4.20. По краям платы для каждой линии скрайбирования должны обеспечиваться технологические заходы для режущего инструмента (вырубку сторонами 2,1х2,1 мм и углом между ними 90°и шириной паза 3,0 мм — пример см. в Приложении А).
4.21. Не допускается располагать радиоэлементы на платах (групповых заготовках) на расстоянии менее 4 мм от внешнего края групповой заготовки (тем более не допускается выступание корпусов радиоэлементов за края групповой заготовки).
4.22. Прямоугольные радиоэлементы (например, керамические ЧИП-компоненты) при размещении вблизи краев печатных плат должны располагаться параллельно (не перпендикулярно!) краю платы.
4.23. Тяжелые навесные компоненты должны располагаться ближе к центру платы, либо уравновешивать друг друга на плате, иначе могут возникнуть проблемы с переворачиванием плат при прохождении в оборудовании.
4.24. Если по краю групповой заготовки располагаются угловые разъемы или другие радиоэлементы, у которых корпус выступает за пределы платы, необходимо спроектировать дополнительное технологическое поле. Вдоль данной стороны платы на дополнительном технологическом поле спроектировать линии скрайбирования и несколько узких прямоугольных отверстий для облегчения операции выламывания единичных плат из групповой заготовки.
4.25. Во избежание попадания припоя на верхнюю поверхность платы не рекомендуется располагать сквозные отверстия диаметром более 6 мм на платах, которые планируется монтировать на установках пайки волной припоя.
4.26. На плате необходимо размещать зоны для идентификационной маркировки (Приложение 1). Зоны маркировки должны быть выполнены белым цветом в слое шелкографии (Silk). Если SMD-компоненты расположены с обеих сторон платы, то зоны маркировки следует проектировать как на верхней (Top), так и нижней (Bot) сторонах.
4.27. В зоне маркировочной метки не должно быть никаких отверстий (переходных, крепежных, фиксирующих, монтажных и т.п.). Под маркировочной меткой предпочтительно иметь однородную гладкую поверхность (слой сплошной металлизации предпочтительнее материала ПП).
4.28. При мультиплицировании плат желательно проектировать маркировочные метки на каждом модуле, только при отсутствии свободного места для размещения метки на модуле допускается проектировать одну общую метку на технологическом поле групповой заготовки. При этом маркировочная метка должна быть расположена вдоль короткой стороны модуля (групповой заготовки).
4.29. Оптимальный размер маркировочной метки 5х30 мм (по согласованию допускаются другие размеры). Минимальное расстояние от края длинной стороны ПП до края маркировочной метки должно быть не менее 3 мм.
4.30. При наличии достаточного места для увеличения информационного поля идентификации модуля необходимо размещать на ПП две маркировочные метки (например, для маркировки № запуска и № платы).
4.31. Ограничения для выбора варианта мультипликации плат:
4.31.1. Минимальное время нанесения паяльной пасты 25 секунд, за это время может быть установлено (значения указаны только в качестве примера).
4.31.2. В случае меньшего числа компонентов на единичной плате желательно производить мультиплицирование плат.
4.32. Основное правило при выборе оптимального варианта мультиплицирования плат: чем меньше ширина мультиплаты, тем выше производительность оборудования поверхностного монтажа. Каждые дополнительные 10 см длины дают потерю 5% производительности. Чем длиннее мультиплата, тем выше производительность сборки, при этом нет ограничивающих по времени факторов оборудования. Другими
словами, для более эффективного использования оборудования оптимально иметь мультиплаты, на которых единичные платы расположены в один ряд либо единичные платы, без мультиплицирования.
4.33. Требования к качеству изготовления печатных плат описаны в стандарте IPC-A-600G (все платы, предназначенные для изделий автомобильной промышленности, относятся к классу 3 данного стандарта).
4.34. Единственно приемлемый уровень качества печатных плат на входном контроле для изделий автомобильной промышленности – 0 дефектов в каждой поставке (по ключевым параметрам, влияющим на безопасность, работоспособность и надежность собираемых изделий, а также на выполнение государственных, законодательных норм).
4.35. При невозможности выполнения любого из перечисленных выше требований необходимо согласовать каждое отступление с ОГТ, специалистами дирекций по закупкам и по качеству.
5. ССЫЛКИ
- РИ «Регламент заказапечатных плат»
- IPC-2221 «Generic Standard on Printed Board Design»
- IPC-2222 «Sectional Design Standard for Rigid OrganicPrinted Boards»
- IPC-2224 «Sectional Standard for Design of PWBs for PCCards»
- IPC-A-600G «Acceptability of Printed Boards»
- IPC-SM-782A «Surface Mount Design and Land PatternStandard»
- ГОСТ Р 53429-2009 «Платы печатные.Основные параметры конструкции»
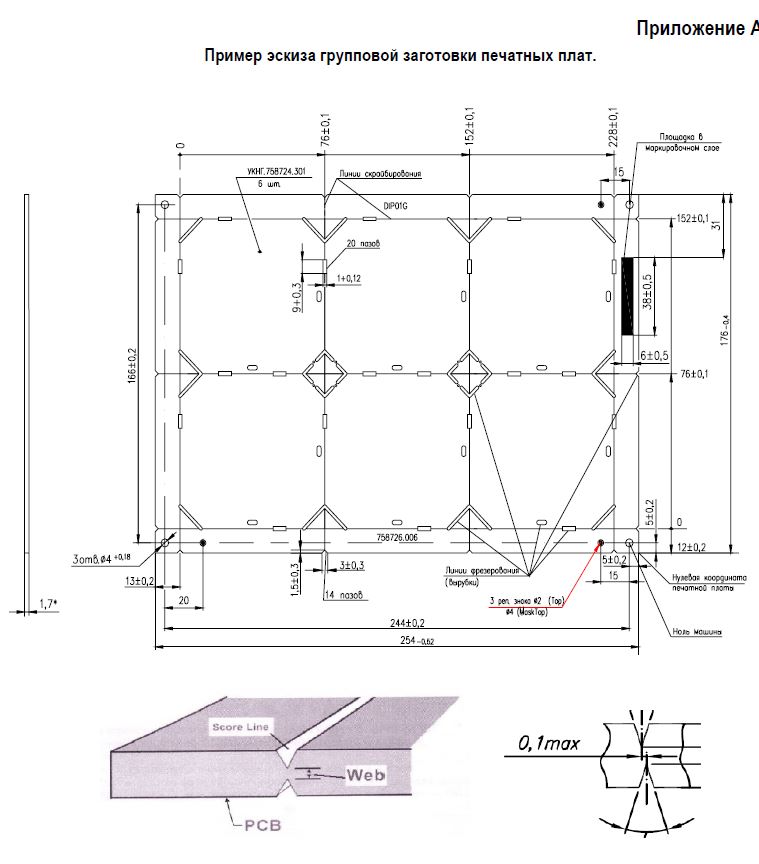